Introduction
Candle Making Machinery refers to the machines used in the manufacturing process of candles. This can include anything from wax melting tanks and mixing chambers, to filling machines and packing equipment. All these machines help to automate the candle production process so that it is faster, more efficient, and more cost effective. The machinery may also help improve the overall quality of finished candles as they are able to provide a continual mix of ingredients ensuring each production run is consistent in size, shape, and colour. The machinery can be used for both hand-crafted and automated candle production.
Benefits of Using Candle Making Machinery
Using candle making machinery can greatly improve the production process for those in the candle-making business. Firstly, it eliminates the need for manual labor, reducing manufacturing costs significantly. Secondly, it increases the speed of production. By using advanced machinery and automated production lines, highly efficient results can be achieved in a fraction of the time needed for manual cutting and assembly. As such, businesses are able to produce large quantities of high-quality candles that meet customer demands quickly and at a cost effective price point. Last but not least, modern candle making machines can create intricate and visually appealing designs that would be too complex to execute otherwise. That makes them ideal for creating boutique candles with intricate patterns or shapes that may require precision work beyond the capabilities of human hands. All these benefits add up to help businesses remain competitive while providing customers something unique and eye-catching they won’t find anywhere else.
Different Types of Candle Making Machinery
There are a variety of candle making machines available on the market today. The type of machine depends on the type of candle being made (i.e. container, block or votive candles).
For container and block candle making, there are two main types of machinery – dipping and pouring machines. Dipping machines make use of molten wax, where the wicks are repeatedly immersed in a wax bath and then re-submerged until the desired thickness is achieved. Pouring machines typically consist of one or more hoppers with electrically heated elements that can pump hot wax into molds to create blocks or pour ice tubs to form pillar candles. These processes both offer precise repeatability for large-scale runs and superior candle quality for popular designs like pillars and containers.
Votive candles also require a different set up ” votive silhouette makers or pour frames are used in this case, as they allow molten wax to be poured directly into individual molds rather than having it placed in blocks or containers. This enables manufacturers to produce highly detailed, intricate shapes far quicker than when using the dipping process alone. Additionally, these systems can feed multiple molds at once while maintaining consistent product sizing over multiple shifts throughout a production run.
Understanding the Components of Candle Making Machinery
Candle making machinery is essential to large-scale and efficient production of candles. The machinery consists of different components, which work together to bring the wax and other materials together to form the desired candle shape. First, there are the melting tanks, which are essential for melting down wax and other ingredients in a controlled environment. Once the raw materials are melted into liquid form, they are pumped into injection molders that can shape the liquid wax into any variety of candle shapes. An automated wicking machine places premeasured lengths of wick into each candle before it goes off to be filled with melted wax or dipped in vats full of colored or scented wax. Lastly, there is a quality inspection component that checks for defects such as color blemishes, air bubbles, and weight discrepancies before the finished candles go out for packaging and distribution.
How to Choose the Right Candle Making Machinery
Choosing the right machinery for candle making can be a challenging process. There are several factors to consider when deciding on the best equipment for your candle manufacturing needs. First, you’ll need to assess the type of candles you are interested in making- whether paraffin, beeswax, or soy wax candles – and select a machine that is suitable for that kind of wax. Second, think about what types of fragrances or design features you’d like to add to your candles and choose a machine that can accommodate them. Thirdly, consider what qualities will make your candle stand out amongst competitors such as choosing an automated machine with a rapid production rate or an adjustable system so multiple molds can be used at one time. Finally, compare prices and review each model’s specifications to ensure it exceeds safety guidelines and meets all of your candle making requirements. Ultimately, selecting the right machinery for candlemaking will depend on your specific business needs and desired outcomes- but armed with this information, you should feel more confident in making the best choice for your operation.
Tips on Buying and Operating Candle Making Machinery
When it comes to candle making, having the right machinery is essential. Candle makers need reliable and efficient machines to produce consistent quality candles quickly and safely. Here are a few tips on how to select and operate the best candle making machinery for your business:
1. Research different types of machinery available: Finding out what types of machinery are available will help you narrow down your choices. Investigate whether one machine can do the job more efficiently than separate machines, or if having multiple accessory machines is necessary for larger scale operations.
2. Compare features: Review features such as double-wicking capabilities, automatic cooling systems, and adjustable speeds that can contribute to improved productivity and better quality candles.
3. Check safety standards: Make sure that any machine you buy meets with safety standards outlined by local authorities in order to prevent injuries or accidents caused by faulty machinery parts.
4. Train staff properly: Before using any machining equipment, always ensure that staff know how to operate them properly and safely. This includes ensuring they understand how many hours of rest they should have between shifts on the machines, how often they should lubricate their machinery parts correctly, and when they need maintenance or repairs done on their equipment.
5. Invest in preventive maintenance: It is important to keep candle making machinery running smoothly by investing in regular preventative maintenance checks conducted by experienced engineers who specialize in working with these types of machines. This will help keep everything up-to-date and reduce long-term costs while improving overall quality control measures within your business operations
Troubleshooting Common Candle Making Machinery Issues
One of the most common issues with candle making machinery is clogged wick pins and needles. If a candle isn’t burning in the desired manner, the wick pins and needles may have become caked with wax buildup or dirt. Often, these can simply be removed by brushing them off with a toothbrush or an old, clean paintbrush and then re-positioned into the machine.
Another frequent problem is what’s commonly referred to as “heat sink”. This occurs when the machine has not had enough time to cool down between uses. Wax particles may stick to hot parts and can cause problems for the wicking process later on. Heat sink should be prevented by allowing an adequate amount of time for cooling and by rubbing off any excess wax from the machine after each use.
Wax buildup in valves is yet another issue that could arise while utilizing candle making machinery. This occurs when wax has hardened and accumulates in a valve that supplies hot melt wax to each mold cavity during production. This can result in inconsistent distribution of molten wax throughout all mold cavities as well as issues such as appearance defects or weak bonding within assembled candles. To prevent this issue, it is important that all valves be cleaned regularly and kept free from buildup of any kind.
Finally, one more issue could arise when several batches are being run simultaneously on the same piece of equipment; batch codes may get placed incorrectly resulting in defective products being produced instead of those intended for that particular run/batch code combination. To avoid this problem it can help to ensure careful record keeping for each run coming through the machinery, including detailed information about batch code locations on each product or corresponding mold set-up which yields high quality products each time without confusion caused by misplaced codes.
Maintenance Tips for Candle Making Machinery
Candle making machinery is an important part of running any candle production business. It is essential to ensure these machines are in good working order and well maintained to ensure continued productivity and efficiency. Here are some top tips for maintaining your candle making machinery:
1. Regularly check the equipment’s components and replace any parts that look worn or damaged. This will help reduce the chances of a breakdown as well as extending the machine’s lifespan in general.
2. Follow all proper maintenance instructions, including lubrication or cleaning down of components when directed by the manufacturer’s guidelines. Not only will this help to protect the warranty on their products but also helps improve overall performance and efficiency.
3. Consider investing in modern upgrades such as automated systems, better insulation, or improved safety features which can help you increase productivity while supporting both long-term cost savings and improved safety conditions for exposed workers.
4. Establish preventative maintenance schedules that include regularly monitoring performance indicators such as temperature readings and chamber pressure checks so you can take remedial action quickly if needed and prevent future costly stoppages/machine damage caused by poor maintenance practices.
5. Hire trained professionals with experience in your particular type of machinery if you need assistance – they can provide valuable advice on how best to maintain and repair the system should any problems arise in the future
Safety Considerations for Candle Making Machinery
Operating any machinery involves potential hazards, so it is important to take precautions when using candle making machinery. One of the most important safety considerations for candle makers is to make sure machinery is treated with caution and handled properly. This includes unplugging machines when not in use, as well as only attaching plugs to machines intended for them. It is also essential to check that all guards are firmly attached and operational and the operators should be wearing appropriate safety items such as goggles and protective clothing. Furthermore, operators should be aware of the correct operation and handling procedures for their specific machine or process they are working with, including routine maintenance and cleaning., Working areas should also be free from debris or obstructions and tools should never be left unattended while running. Lastly, a fire extinguisher must be readily available in case of a fire hazard due to combustible materials being used in the candle-making process.
Candle Making Machinery
Candle making machinery has come a long way from its humble beginnings. Today, advances in technology have made the craft more accessible and easier than ever before. In the coming years, we can expect to see even more modern tools and technologies that make candle production simpler, faster and more efficient. Some possible advancements include automated wax-melting machines that reduce time spent melting wax, 3D printers that make creating intricate shapes simple, or computerized temperature control systems designed to keep candles burning at optimal temperatures. With advances in technology and materials, there’s no limit to what can be achieved with candle manufacturing equipment. As demand grows for innovative candles, so too will the need for machinery capable of meeting modern needs.
Wrapping Up
Investing in candle making machinery has many advantages. By investing in the necessary machinery and equipment, one can easily streamline their production process and significantly increase their output. Candle makers can produce more candles faster and with higher profits, meaning a quicker return on investment. Furthermore, the demand for handmade candles is growing as customers are increasingly looking for high-quality candles that are made in an environmentally friendly manner. Investing in machinery to produce candles gives candlestick makers new opportunities to reach untapped markets, potentially increasing sales and revenue. Additionally, capital investments of this kind will require less time spent on manual labor and allow staff to focus more intensely on other activities needed to promote growth such as marketing and customer service, which can lead to increased customer satisfaction and brand loyalty. In summary, investing in candle making machinery is a wise choice as it has the potential to improve production processes, increase revenue and open up new growth opportunities. With careful planning, a well-implemented strategy and good business acumen, buying the right candle-making machine for your needs will be beneficial for any business.
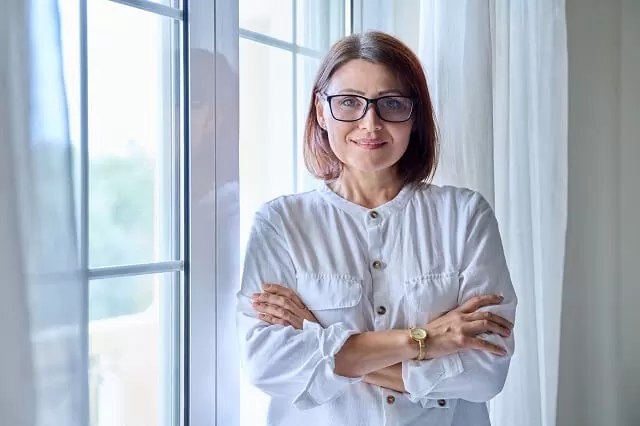
Welcome to my candle making blog! In this blog, I will be sharing my tips and tricks for making candles. I will also be sharing some of my favorite recipes.