Candle making is an age-old craft that has captivated and intrigued people for centuries. The process of creating a beautiful, fragrant candle is not only a therapeutic and creative endeavor but also requires a deep understanding of various terminologies specific to the craft. In this article, we will explore the importance and fascination of candle making terminologies, shedding light on their significance in creating high-quality and safe candles.
For those new to candle making, it may come as a surprise that there is an entire language associated with this art form. But for experienced candle makers, these terminologies are part of their everyday vocabulary. From basic terms like wick, melt pool, and fragrance load to more advanced concepts such as tunneling, cold throw, and hot throw, understanding these terminologies is crucial to mastering the craft.
At its core, being familiar with candle making terminologies allows artisans to communicate effectively within the community and learn from one another’s experiences. It enables beginners to follow instructions accurately and troubleshoot any issues they may encounter along the way. Moreover, having a comprehensive knowledge of these terms empowers candle makers to experiment with different techniques and ingredients confidently.
In the upcoming sections of this article, we will delve into various categories of candle making terminologies. We will explore must-know basics for every candle maker as well as advanced concepts for seasoned experts. Additionally, we will discuss essential tools required for successful candle making and unravel the scientific aspects behind certain terminologies.
Furthermore, pro tips for mastering these terms will be shared along with common mistakes to avoid. Finally, we will explore unique techniques using specific terminologies alongside step-by-step examples.
By the end of this article, you would have gained a deep understanding of numerous candle making terminologies that are necessary for creating high-quality candles while ensuring safety at every step. So let’s embark on this fascinating journey into the world of candle making terminology.
What Are Candle Making Terminologies
Candle making is not just a simple craft; it is an art that requires knowledge and understanding of various terminologies. These terminologies are used to describe different aspects of the candle making process, from the materials and tools used to the techniques employed. In this section, we will delve into a comprehensive explanation of what candle making terminologies are and why they are important.
Defining Candle Making Terminologies
Candle making terminologies refer to the specialized vocabulary and terms used within the candle making industry. These terms are essential for communicating ideas, techniques, and concepts related to the craft. They help candle makers understand instructions, troubleshoot issues, and create high-quality candles.
Candle making terminologies encompass a wide range of topics, including materials, tools, techniques, and troubleshooting. Some common examples include wick, melt pool, fragrance load, tunneling, cold throw, hot throw, thermometers, pouring pots, flash point, saponification, frosting, wet spots, sinkholes, layering swirling, embedding – just to name a few.
The Importance of Candle Making Terminologies
Understanding candle making terminologies is crucial for several reasons. Firstly, knowing these terms allows candle makers to effectively communicate with others in the industry. By using correct terminology when discussing techniques or troubleshooting issues with fellow enthusiasts or suppliers alike ensures clear communication without confusion.
it is vital for ensuring safety in candle making.
Certain terminologies like flash point (the lowest temperature at which a substance can vaporize to form an ignitable mixture) are crucial in understanding how to handle materials safely and prevent accidents such as fires or explosions during production or burning of these candles.
terminology plays an integral role in improving skills.
By comprehending complex terms such as saponification (the chemical reaction between fats/oils and alkali that produces soap), candle makers can gain a deeper understanding of the science behind their craft. This knowledge empowers them to experiment with different techniques, troubleshoot issues, and create unique and high-quality candles.
Basic Terminologies Every Candle Maker Should Know
When it comes to candle making, there are several key terminologies that every candle maker should be familiar with. Understanding these basic terms is crucial for producing high-quality candles that burn properly and emit the desired fragrance. In this section, we will explore three important terminologies that every candle maker should know: wick, melt pool, and fragrance load.
The wick is an essential component of a candle as it is responsible for facilitating the burning process. It consists of a braided or twisted thread made from materials like cotton or paper. The size and type of wick used in a candle greatly impact its performance. Choosing the right wick for your specific candle is crucial to ensure proper burning, prevent tunneling, and achieve an even melt pool.
The melt pool refers to the liquid wax that forms as the candle burns. It is important for the melt pool to reach the edges of the container to avoid tunneling (uneven burning) and wasting wax. The depth of the melt pool also affects the scent throw of the candle.
A shallow melt pool may result in a weaker fragrance while a deep melt pool can lead to excessive soot formation. Candle makers must carefully select their wax blend and wick size to achieve an ideal melt pool depth.
Lastly, fragrance load refers to the amount of fragrance oil added to the wax during the candle making process. It determines how strong or subtle the scent will be when the candle is burned. The appropriate fragrance load depends on factors such as the type of wax used, container size, and personal preference. Using too much fragrance oil can lead to performance issues like smoking or poor burn quality, while using too little may result in a weak scent throw.
Understanding these basic terminologies allows candle makers to make informed decisions throughout each step of their craft. From selecting the right wick for their candle to achieving the desired scent throw, mastering these terms is essential for creating candles that burn evenly, emit a pleasing fragrance, and provide an enjoyable experience for users.
Term | Definition |
---|---|
Wick | A braided or twisted thread made from materials like cotton or paper, responsible for facilitating the burning process in a candle. |
Melt Pool | The liquid wax that forms as the candle burns; it should reach the edges of the container to avoid tunneling and wasting wax. |
Fragrance Load | The amount of fragrance oil added to the wax during candle making; determines the strength of the scent when burned. |
Advanced Terminologies for Candle Making Experts
Candle making enthusiasts who have mastered the basic terminologies are ready to explore more advanced concepts in the art of candle making. This section will delve into three important advanced terminologies that every candle maker should be familiar with: tunneling, cold throw, and hot throw.
Tunneling
Tunneling is a common issue that candle makers face when their candles burn unevenly, leaving a hole or tunnel in the middle. This occurs when the outer edges of the candle do not completely melt and pool all the way to the edge during each burn. The melted wax then accumulates in a ring around the wick while leaving an untouched inner core of solid wax.
To prevent tunneling, there are several factors to consider. First, selecting an appropriate wick size is crucial as it plays a significant role in achieving an even burn. Additionally, optimizing burn time by allowing candles to burn long enough so that the melted wax reaches all edges is essential. Candle makers should also avoid placing their candles in drafty areas as this can contribute to uneven burning.
Cold Throw and Hot Throw
When discussing fragrances in candle making, two important concepts come into play: cold throw and hot throw. Cold throw refers to the strength of a fragrance when it is unlit or not burning. It determines how well a scent disperses throughout a room without any heat or flame involved.
Hot throw, on the other hand, refers to the strength of a fragrance when it is lit or burning. It describes how intense and noticeable the scent becomes as the heat from the flame vaporizes oils from the heated wax.
Achieving a desirable balance of cold throw and hot throw involves careful selection of fragrance oils and understanding their performance at different temperatures. Experimenting with various scent load percentages can help candle makers find the perfect combination for optimal scent strength and longevity.
Understanding these advanced candle making terminologies is vital for experienced candle makers as they strive to create high-quality candles with exceptional fragrance performance. By mastering tunneling prevention techniques and finding the perfect balance between cold throw and hot throw, candle makers can elevate their craft to new levels of expertise.
Must-Have Tools for Candle Making
The tools and equipment used in candle making play a crucial role in ensuring that the candles are made correctly and safely. Understanding the purpose and function of these tools can greatly enhance the candle making process. Three must-have tools for candle making are thermometers, pouring pots, and wick trimmers.
Thermometers
A thermometer is an essential tool for candle makers as it helps to monitor and control the temperature during different stages of the candle making process. The two most commonly used thermometers in candle making are:
– Candle Making Thermometer: This thermometer has a sharp, pointed tip that allows it to be inserted into the wax to measure its temperature accurately. It is important to use a thermometer specifically designed for candle making, as regular cooking or candy thermometers may not be suitable.
– Infrared Thermometer: This non-contact thermometer measures the temperature by detecting infrared energy emitted from the surface of the wax. It allows for quick and easy temperature readings without having to come into direct contact with hot wax.
Having an accurate thermometer is crucial because each type of wax requires specific temperature ranges for melting, adding fragrance oils, and pouring into molds. This ensures that the candles will have proper burn characteristics and longevity.
Pouring Pots
Pouring pots, also known as melting pots or double boilers, are containers specifically designed for melting wax and pouring it into molds or containers. They play a vital role in maintaining a safe and controlled environment during the candle making process. There are two main types of pouring pots:
– Stainless Steel Pouring Pot: Made from durable stainless steel, this type of pouring pot is commonly used by both amateur and professional candle makers. It has a long handle that stays cool while heating to prevent burns.
– Aluminum Pouring Pot: These pots are lightweight yet sturdy. They heat up quickly, allowing for faster melting times.
Pouring pots usually come in different sizes, and it’s important to choose a size that can accommodate the amount of wax you will be melting. They also often feature a spout or lip for easy pouring into molds without spilling.
Wick Trimmers
Wick trimmers are small tools used to trim the wicks of candles before lighting them. Properly trimmed wicks help achieve an even burn, prevent excessive smoking, and reduce soot buildup. Common types of wick trimmers include:
– Straight Wick Trimmers: These trimmers have a straight design with a cutting mechanism that helps easily trim the wick.
– Angled Wick Trimmers: With angled blades, these trimmers make it easier to reach and trim the wick in jar candles.
Using wick trimmers before each burn ensures that the flame height is controlled and prevents mushrooming at the tip of the wick. This ultimately leads to cleaner burning candles with minimal smoke and longer burn times.
Knowing how to effectively use these essential tools can greatly enhance your candle making experience and improve the quality of your finished products. By investing in reliable thermometers, pouring pots, and wick trimmers, candle makers can create candles that not only look beautiful but also burn safely and efficiently.
Tool | Function |
---|---|
Thermometers | Measure and control temperature during different stages of candle making process. |
Pouring Pots | Melt wax and pour it into molds or containers. |
Wick Trimmers | Trim candle wicks before lighting for even burning. |
The Science Behind Candle Making
Candle making is not just an art, but also a science. Understanding the scientific aspects of candle making can greatly enhance the quality and safety of your candles. In this section, we will delve into some important terminologies related to the science behind candle making.
1. Flash Point: The flash point refers to the minimum temperature at which a substance gives off sufficient vapor to ignite in the presence of an open flame or spark. It is a crucial term to understand because different waxes have different flash points.
For example, paraffin wax has a higher flash point compared to soy wax. It is important to use caution when working with waxes that have lower flash points, as they are more likely to ignite.
2. Saponification: Saponification is a chemical process that occurs when fats or oils react with an alkali (such as lye) to produce soap and glycerin. Although saponification is not directly related to candle making, it is important for those who make their own candle molds. When using materials like silicone molds or plastic containers, it is essential to check whether they are resistant to saponification caused by the candle ingredients.
3. Soy Wax: Soy wax is a popular choice among candle makers due to its natural origins and clean burning properties. Made from soybean oil, soy wax has gained popularity as an eco-friendly alternative to paraffin wax. Its low melting point allows for longer burning times and better fragrance release.
Pro Tips for Mastering Candle Making Terminologies
Mastering candle making terminologies is essential for creating high-quality and safe candles. In this section, we will provide you with some pro tips on how to achieve proper cold and hot throws, prevent tunneling, and control fragrance load.
Achieving a proper cold throw is crucial as it determines the scent strength of your candle when it is not lit. To enhance the cold throw, make sure to use the appropriate fragrance load. The fragrance load refers to the amount of fragrance oil used in proportion to the wax. It is recommended to follow the manufacturer’s guidelines for fragrance load recommendations. Additionally, using a high-quality fragrance oil can significantly impact the cold throw of your candle.
On the other hand, achieving a proper hot throw is vital as it ensures that your candle emits a strong and pleasant scent when lit. Proper wick selection plays a key role in achieving a good hot throw. The size of the wick should be suitable for the diameter of your candle container.
Using a wick that is too small may lead to poor hot throw, while a wick that is too large can lead to excessive heat or even safety issues. Utilize resources such as wick charts or seek advice from experienced candle makers to determine the right wick size for your specific candle.
Tunneling is a common issue that occurs when wax burns down only in the center, leaving a tunnel-like cavity around the wick. To prevent tunneling, ensure that you trim your wick properly before each burn session. A longer wick tends to produce more heat and can cause uneven melting. Additionally, allowing your candle to burn long enough during each lighting session helps prevent tunneling by ensuring that all of the wax melts evenly across the entire surface.
By following these pro tips and mastering candle making terminologies related to achieving proper cold and hot throws, preventing tunneling, and controlling fragrance load, you can create candles that not only look beautiful but also provide a delightful scent experience.
Common Candle Making Mistakes and How to Avoid Them
Mistakes can happen in any craft, and candle making is no exception. However, by understanding common candle making mistakes and how to avoid them, you can improve your candle-making skills and create high-quality candles. There are several troubleshooting terminologies that every candle maker should be familiar with, including frosting, wet spots, and sinkholes.
Frosting is a phenomenon where a white powdery layer appears on the surface of the candle. It occurs when the wax cools too quickly during the curing process. Frosting does not affect the performance of the candle but might be undesirable for aesthetic purposes. To prevent frosting, it is important to maintain a moderate pouring temperature and ensure that your candles cool slowly and evenly.
Wet spots refer to air pockets that form between the container walls and the wax as the candle cools down. These patches can be unsightly and may also cause uneven burning. Wet spots occur due to poor adhesion of the wax to the container surface. To prevent wet spots, it is crucial to preheat your containers before pouring hot wax into them. Additionally, ensuring a slow cooling process without rapid temperature changes can help minimize wet spot formation.
Sinkholes are indentations or cavities that develop in candles during cooling or burning. They occur when there is excessive shrinkage of wax around the wick area as it cools down. Sinkholes not only affect aesthetics but can also negatively impact burn performance by inhibiting proper oxygen flow to sustain a consistent flame. To avoid sinkholes, it is important to pour your candles at the correct temperature, utilizing techniques like double-pouring or topping up after cooling has begun.
By being familiar with troubleshooting terminologies like frosting, wet spots, and sinkholes, you can identify potential issues before they occur and take appropriate preventative measures during your candle-making process. Through careful attention to detail and incorporating these tips into your craft, you can create beautiful candles that burn evenly and possess a professional finish.
Exploring Unique Candle Making Techniques
Candle making is not only about creating beautiful and fragrant candles; it also offers an opportunity to explore unique techniques that can enhance the visual appeal of your creations. Layering, swirling, and embedding are three popular techniques that can take your candle making skills to the next level. In this section, we will delve into these techniques and discuss the terminologies associated with them.
Layering is a technique where different colored or scented wax layers are poured one on top of another to create stunning visual effects within the candle. It involves pouring each layer of wax at specific temperatures to ensure proper adhesion and prevent separation.
The temperature at which you pour each layer depends on various factors such as the type of wax being used and the desired effect. It’s important to note that during layering, you need to allow each layer to cool and harden before pouring the next one.
Swirling is another captivating technique that adds a touch of artistry to your candles. This technique involves creating patterns by gently swirling different colored or scented wax together in the container or mold. To achieve swirls, you can use a skewer or a chopstick to lightly drag or swirl the colors around while they’re still fluid.
It’s important to be mindful of how much you swirl as too much swirling may result in muddy colors instead of distinct patterns. Practice patience and experiment with different methods until you achieve your desired swirl effect.
Embedding is a technique where decorative elements such as floral petals, dried herbs, small trinkets, or even other smaller candles are added within the main candle structure. To embed objects successfully, it’s essential to choose items that are heat-resistant and won’t melt when exposed to high temperatures for prolonged periods.
When embedding objects within a candle, make sure they are properly centered and that they won’t move during pouring and solidification. You can use a wick sticker or a dab of melted wax to secure the embedded objects in place.
To help you understand these techniques better, let’s walk through step-by-step examples of layering, swirling, and embedding. We will start with layering, where we will guide you on how to create a beautiful ombre effect using different shades of blue wax.
Then, we will move on to swirling, providing detailed instructions on how to create exquisite swirl patterns using contrasting colors. Lastly, we will explore embedding, demonstrating how to add dried rose petals within a soy wax candle for an elegant touch.
By mastering these unique candle making techniques and familiarizing yourself with the associated terminologies, you can unleash your creativity and produce candles that are not only visually stunning but also offer an enchanting experience when lit. So grab your supplies and get ready to dive into the world of layering, swirling, and embedding to take your candle making skills up a notch.
Conclusion
In conclusion, understanding candle making terminologies is essential for creating high-quality and safe candles. As we have discussed throughout this article, candle making involves a wide range of specific terms and concepts that are crucial to master in order to produce successful results.
By familiarizing yourself with basic terminologies such as wick, melt pool, and fragrance load, you can ensure that your candles burn evenly and release the desired scent. Additionally, advanced terminologies like tunneling, cold throw, and hot throw allow experienced candle makers to troubleshoot issues and fine-tune their craft.
Having the right tools for candle making is also vital. Thermometers help monitor temperatures to achieve optimal wax melting and pouring conditions. Pouring pots provide controlled pouring while wick trimmers maintain proper wick length for a clean and efficient burn.
Understanding the science behind candle making through terms like flash point, saponification, and soy wax enables you to make informed decisions regarding wax selection, fragrance choices, and safety measures.
Finally, by mastering troubleshooting terminologies such as frosting, wet spots, and sinkholes, you can address common candle making mistakes and avoid them in your future creations.
Overall, acquiring knowledge of candle making terminologies empowers you as a candle maker. It not only helps you produce high-quality candles but also ensures the safety of your products. By continually expanding your understanding of these terms and applying them effectively in your practice, you can take your candle making skills to new heights.
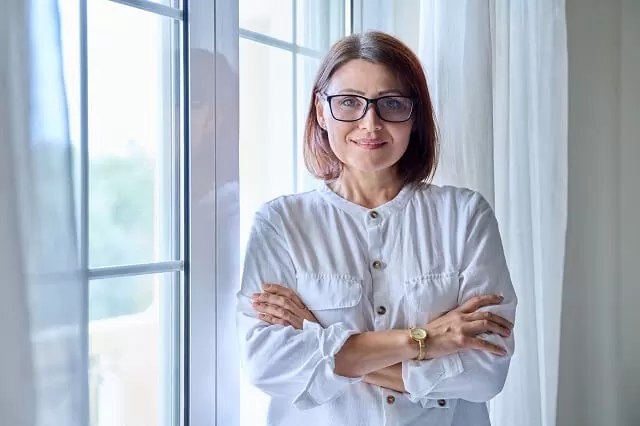
Welcome to my candle making blog! In this blog, I will be sharing my tips and tricks for making candles. I will also be sharing some of my favorite recipes.