Introduction
Candle mold making from sculptures is an interesting and creative activity that has gained popularity in recent years. It is a way to create unique, one-of-a-kind candles with a design of your own choosing. From animals to flowers and geometric shapes, almost anything can become a candle when done correctly. Candle mold making involves three basic steps: creating a sculpture, casting it in plaster, and filling it with melted wax. To finish the candle, you must arrange wicks in the mold, heat the wax until it’s completely liquid, pour the wax into the Plaster of Paris cast, and once cool trim off any excess wax on top. After allowing time for cooling and hardening, you will have your very own unique sculpture candles to light up your room!
Safety First
Before you begin the candle mold making process, there are some important safety precautions to take. Firstly, ensure that the environment that you will be working in is as safe and well ventilated as possible. Make sure that all materials used in the process of making the molds are properly sealed and packaged to protect against any potential reactant or allergen contact. Wear protective gloves and safety glasses while handling hot wax or other chemicals involved in the process. Finally, never leave a lit candle unattended and always extinguish candles after use to avoid accidental fires. Taking these safety steps will help guarantee that while you work with your molds, you remain protected from any potential hazards.
Supplies Needed
Essential supplies and tools are needed to successfully make candles using a mold. Below is a list of necessary supplies:
1. Table or bench-top sculpture- A 3D model of an object that can be replicated in the molding process.
2. Wax or Candle Molds- These come in various shapes and sizes depending on the complexity of the design. They also require special materials for releasing the casting from the molds with no damage to it.
3. Heat Source- Use either double boilers, microwaves, ovens, or even heat guns depending on what type of wax is used in your project.
4. Release Agent- Spray releases agents or mixes like Vaseline can guarantee that your molds are released without any damage or distortion to your workpiece.
5. Mold Clamps/Steel Strip” Ensure that temperatures stay uniform while hardening and prevent overflow while forming your candle mold by using steel strip clamps around edges of the molds when necessary and helpful for small pieces that require more attention during cooling process without causing stress to them once wax have been removed form the molds fully cured up and hardened after cool down following pour phase occurred before extraction stage with help from release agent already applied within walls placement around pieces before start up procedure into cooling down phase following next step before finishing touches added prior completion stage reached soon enough afterwards
Getting Started
1. Select a sculpture. Choose something that is smaller in size and made from a material that is safe for candle making. Wax and metal sculptures are the most common choices for this type of project.
2. Carefully remove the sculpture from its original base or holder, if applicable. Make sure to do this very carefully so as to not damage the sculpture in any way.
3. Clean the sculpture with a damp cloth to remove any dust or debris that may have accumulated during storage or travel. This step helps ensure a smooth wax cast later on in the process.
4. Examine the sculpture closely and decide which parts you would like to feature in the final candle product, such as facial features or other distinguishing characteristics of the artwork.
5. Apply an oil-based coat of sealant to areas you wish to preserve when creating molds of your selected design elements so they remain intact throughout the candlemaking process; typically, an artist’s sealant works best for this purpose..
6. Determine where you want to make incisions into the sculpture in order to create custom pieces for candle molding; try choosing places for access points along natural crevices or other indentations in sculpted sections that are form-fitting with your chosen design elements without cutting away too much material and sacrificing detail quality.
7. Use specialized tools intended for carving and whittling when making incisions into your scultpures, avoiding using regular kitchen knives to prevent potential mishaps during delicate carving processes; additionally, remember safety cautions when working with sharp objects such as keeping fingers and hands away from blades at all times while creating wax molds!
Crafting the Candle Mold
Candle mold making from sculptures can be an incredibly rewarding and creative experience. It is important to know the techniques and tools required to add variations and details to your candle mold in order to achieve the desired results. One of the biggest factors that will affect your finished product is the wax type you use. Most people start by using one-piece molds made of a combination of clay, plaster, or silicone rubber. Some more experienced craftspeople may opt for a multi-piece mold consisting of separate pieces for each layer of wax needed to complete their design.
Once you have determined the shape and design you need for your candle mold, there are several methods available for adding detail and texture. Beginners should practice building up different layers with clay or textured plastic sheets before trying out more intricate techniques like sculpting with an epoxy mixture or carving with a hot knife tool. Carving blades, rotary tool attachments, small hand tools such as files and rasps, and brushes can all be used to create intricate designs on your candle molds. Painting techniques can also be employed once the surface is cleaned up, providing further variation and color to your finished product. Pre-made textures such as lace patterns can also be used to create unique shapes in wax candles without having to use additional tools or materials. Making sure that all surfaces are properly sealed is key when using pre-made textures with wax as they will increase exposure to heat during pouring.
Finishing Touches
Candle mold making from sculptures can be completed with certain finishing touches to achieve a smooth surface and fine detailing. Various materials are available on the market that can help smooth out the contours of the candle mold, such as polymer clay, wax-based mediums, and flexible silicone rubber. Polymer clay is easy to work with because it becomes soft and pliable when warmed, allowing for easier maneuvering of the material’s shape in order to create more intricate details onto the candle mold. Wax-based mediums also provide sculpting flexibility while providing a glossy finish; they could be either wiped onto or brush painted over the candles before they are set into molds. Lastly, flexible silicone rubber allows users to obtain exact replicas of model statues or figurines since it maintains its original shape even when pressed into molds. With these three choices manufacturers have various options at their disposal that enable them to generate perfectly formed candle molds with an immaculate finish.
Finishing Up
After the candle mold is created from the sculpture, it is important to care for and store it correctly. For best results, work in a clean home environment and remember that the room should ideally be at least 20 degrees Celsius. To prevent sticking of the wax to the mold, rub a thin layer of petroleum jelly onto it and leave for one hour before pouring in molten wax. When not in use, store the candle molds in an air-tight container or bag filled with silica gel to help wick away any moisture, as excess moisture can corrode materials over time. Additionally, avoid subjecting your candle molds to extreme temperatures, solvents or any acids that could cause damage or compromise their shape and size over time. Finally, regular cleaning with warm water and a little mild soap is key ” especially after each use ” in order to maintain the integrity and longevity of your sculptures-turned-candle molds.
Conclusion
Making a candle mold from sculptures offers many unique advantages. When you make molds from sculptures, you have greater control over the design and shape of the finished product. This allows for more creative freedom and customization in your candles. Additionally, by using sculpted molds, you can produce an infinite variety of sizes, shapes, and designs that will give your candles a beautifully sculpted look. Lastly, when you use sculpted molds to create candles, there are fewer levels of thermal shock and they are usually resistant to cracking and breaking due to the already hardened material they are made out of. This greatly reduces the chances of damage during pouring or cooling phases and ensures a satisfactory end result with each casting. These benefits combine to make candle mold making from sculptures a great choice for any experienced craftsperson looking to take their candle artistry to the next level.
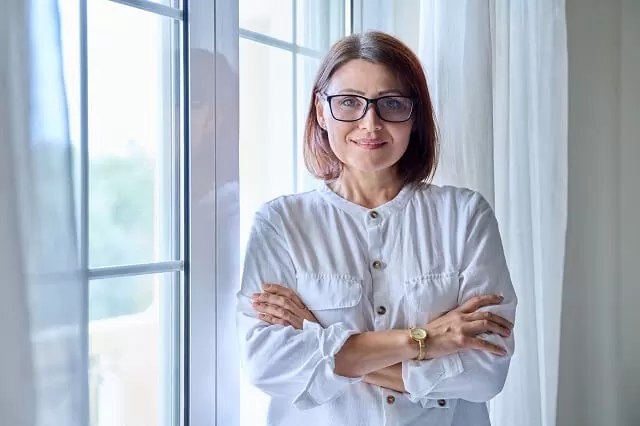
Welcome to my candle making blog! In this blog, I will be sharing my tips and tricks for making candles. I will also be sharing some of my favorite recipes.