Introduction
The rise of the candle making machine in the 1800s was an important development for the modern industrial age. By streamlining and automating a laborious and time-consuming process, candle machines allowed manufacturers to produce candles quickly and efficiently. This revolutionized the way people consumed the product, from small households to churches and other large organizations.
These large scale, eight place candle making machines were powered by steam engines or water wheels and featured an automated system which could create twelve candles per minute. During this era, only four machines were built in different parts of England. The manufacturers aimed to make these highly efficient machines compatible with every kind of wax available on the market at that time; as a result, some modifications were done on each machine such as dissolving waxes or oils in order to reach a customer’s desired quality.
Because these larger machines required a great investment in resources, they were primarily owned by large companies eager to benefit from their economies of scale. Candle makers of medium and smaller size were mostly unable to afford this technology and had to resort either to manual production or lighter machinery such as four place candle moulds.
Notwithstanding, the eight-place machine served as one of many turning points for industrialization during this period of great progress; it provided higher productivity than any other method in use before its invention. Its potential usage was realized through its widespread acceptance from those who used it to train employees and provide more employment opportunities within the industry itself.
Types of Candle Making Machines Available During the 1800s
In the 1800s, there were a variety of candle making machines available. Some machines featured eight places, with each place being used to hold and feed a wick into molten wax. Many of these machines even used ribbon-like wicks to help candles last longer and burn brighter. Other machines featured rotary molds which allowed for the mass production of candles in various shapes, sizes and colors. In addition, some candle making machines used wax centrifuges to filter impurities from raw wax and force air into the wax for easier molding processes. Lastly, dipping tanks were available for dipping or manual rolling techniques to form candles faster than ever before.
Historical Timeline of Candle Making Machine Development
1800s: The first candle making machine was invented in 1833 by French inventor, Jacques Louis Cavey. The eight place candle making machine he invented allowed the user to create up to eight candles at one time. It utilized a simple system of wooden molds that were placed into a large copper pot full of molten tallow or wax, where they would be left until they cooled and solidified in the molds. This machine revolutionized the handmade candle industry and led to increased production in factories.
1840s: In 1840, Danish inventor Jens Fries patented a similar machine which employed a movable iron mould with multiple chambers for pouring the molten liquid. Machines like this made producing candles much faster than ever before, allowing for an increase in production volume and quality.
1850s: Further developments occurred throughout the 19th century. In 1857, William Battles proposed an improved version of Cavey’s original machine with multiple rows and separate compartments for pouring wax into each of the molds. This innovation allowed for more efficient production and gained widespread attention from manufactures who saw its potential profitability.
1900s: Candle making machines continued to evolve through the 20th century with advancements like steam injection technology which allowed workers to control pressure and temperature more accurately during production processes. By this point, candle makers used machines such as presses and dipping tanks which are still used today but are mostly automated by robotics instead of human labor.
Features of Eight Place Candle Making Machines
The eight place candle making machines of the 1800s typically had several features. They often included up to eight cast iron columns made with separate carriages which allowed for more efficient production as many people could work on the eight candles at once. The manual lever handles came with a controlled stopping point that ensured the correct length and thickness of each candle. An adjustable handle helped control the flow of wax from each carriage, nicknamed ‘cups’ by those who used them, so that each partition was filled evenly. Multiple wick holders held cotton wicks in place while they were being dipped into the heated wax so they could be shaped accurately. The machines also featured an adjustable clutch, allowing all of the carriages to be moved together which further increased efficiency in industrial production settings. The entire machine was able to be moved by special transport handles as needed or locked in place with straps to keep it stationary while workers produced candles in bulk.
Advantages of Eight Place Candle Making Machines
The Eight Place Candle Making Machines of the 1800s were powerful and helpful tools that allowed candle makers to manufacture more candles in a shorter period of time. The machines improved upon hand-poured methods by providing a quicker and more efficient way to produce rounded, cylindrical candles. The machines could produce two or three times as many candles as individuals could make in the same amount of time, allowing businesses to expand their output and leading to greater profits. With this tool, the industrialization of candle production was finally possible. Not only did it allow manufacturers to keep up with demand, but also provided more consistent sizing, quality, and shape from one batch to the next. In addition, productivity improvements meant that smaller utilities — such as churches and households — could now access high-quality candles at reduced prices. As such, the Eight Place Candle Making Machine revolutionized the industry throughout America during this period and beyond.
Disadvantages of Eight Place Candle Making Machines
Eight place candle making machines used in the 1800s were primitive, labour-intensive and hazardous. The machines operated by a single person at a time and had no safety mechanisms. A well-trained operator was needed to ensure maximum efficiency with the machine. Additionally, due to the lack of automation, considerable amounts of wax were wasted during operation and the eight places only allowed for eight candles to be made at once, a slow process compared to modern candle-making technologies which can produce hundreds of candles per minute. Furthermore, high temperatures were required for larger batches of wax resulting in fire hazards if left unattended for too long.
Inspiring Designs of Eight Place Candle Making Machines
In the 1800s, an incredible invention was created to revolutionize the candle making industry – the Eight Place Candle Making Machine. Designed by craftspeople with a keen eye for innovation and efficiency, these machines helped to quickly make large amounts of candles in one go, expanding businesses and factories alike. Eight place candle machines boosted productivity tenfold with its intricate designs that made it possible to shape up to eight individual pillar candles simultaneously. This opened up a wide variety of creative freedom as craftspeople could use their imagination to create all new shapes and sizes, whilst also experimenting with different types of wax and colors. Additionally, with precision calibrations, these machines enabled users to select exactly how tall or short, thick or thin they wanted their candles to be. Amazingly enough, some of the Eight Place Candle Making Machines from this era still exist today, showing off incredibly well-designed parts such as handcrafted wick holders and height adjustable molds. These inspiring pieces of engineering were indeed crucial for the candle making industry in the 19th century – allowing craftspeople to hone their skills and diversify their skillset into something unique – truly revolutionizing how business was done!
Examples of Notable Eight Place Candle Making Machines from the 1800s
1. The Blakeslee and Warren Machine – this candle making machine was patented in 1856 by Samuel S. Blakeslee and Lucius A. Warren. It could produce up to 400 candles per hour, making it one of the fastest machines of its kind at the time.
2. The Siemens & Halske Type K Candle Maker – this machine was developed in 1884 by Werner von Siemens and Edward Halske, two German electrical engineers. It had a unique construction, with three separate divisions for different processes: dipping, sizing, and cooling. It could turn out around 8000 candles an hour, and it became an industry standard for many years afterward.
3. Sherwood’s Machine – invented in 1885 by William Sherwood Jr., this machine used molds rather than dipping wicks into wax to form the candles’ shape. This allowed them to be made consistently and quickly, with a rate of up to 80 per minute on average across all sizes produced by the machine.
4. Merrick’s Automated Candle Maker – first developed in 1886 by James Coston Merrick, this machine featured multiple compartments which alternately dried and filled as well as controlled temperatures so that the same amount of wax came out each time a new candle formed. It could produce up to 80 two-inch candles an hour or 40 seven-inchers per minute across its length of twenty inches of moulds set side-by-side.
Summary
Eight place candle making machines first appeared in the 1800s, revolutionizing the way wax candles were produced. This type of machine would have allowed for faster and more efficient production than that of hand-making each candle separately. In addition, it also resulted in a much higher quality product due to automation. Eight place machines are a type of continuous thread wicks manufacturing equipment. They featured eight spindles protected by an adjustable guard and rubber tapping plate that was used to shape the wax into an even column. The thread was attached to these spindles which were then dragged across a heated chamber or applied pressure while they melted. Afterwards, they would be cut off with any residue wax scraped off into a molten container. Special tools could be added to increase the speed and efficiency of production.
This invention made mass production of higher quality candles possible and greatly reduced labor costs associated with candle making. It also opened up opportunities for those in the industry, allowing for new innovations that contributed to better products and larger profits. Candle makers around the world can thank this machinery for making the process much easier and more efficient than before!
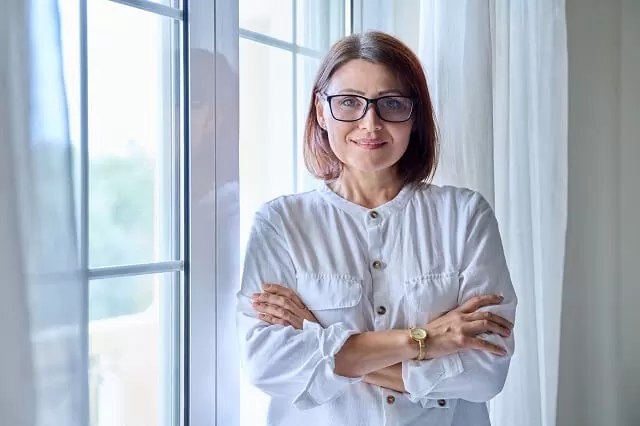
Welcome to my candle making blog! In this blog, I will be sharing my tips and tricks for making candles. I will also be sharing some of my favorite recipes.