Introduce the concepts of sustainable and eco-friendly candle making
Sustainable and eco-friendly candle making is an important part of the modern candle industry. As consumers become more conscious about their environmental impact, businesses that manufacture candles must strive to make the process of making them as sustainable as possible. In many cases, this means using natural materials that are renewable, recyclable, and biodegradable.
One of the major advances in candle making processes when it comes to sustainability has been switching from traditional paraffin wax to vegetable-based or soy waxes. These newer types of wax can be made more naturally with fewer chemicals than paraffin wax and are better for the environment overall. Additionally, beeswax has become increasingly popular amongst environmentally conscious consumers as a natural, renewable source of wax for candle production.
As a candle making equipment manufacturer, you can encourage sustainable practices among your customers by suggesting they use eco-friendly materials in their products and providing guidance on recycling/ reuse efforts within their business operations. Furthermore, you can provide support to those who wish to reduce their carbon footprint by offering energy efficient manufacturing equipment fueled by renewable sources such as solar power!
Discuss safety measures
Candle Making Equipment Manufacturers take a variety of safety measures to ensure their products are safe and can be used without worry. These safety measures range from placing reflective safety stickers on the equipment to using only heat-resistant materials when constructing them. Some manufacturers may also include a warning label with important information about candle making, such as the optimal distance for burning and how to properly extinguish candles. Furthermore, the use of child-resistant lids or secure lids could be used in order to prevent curious children from accessing the containers and being burned or injured. Furthermore they might perform rigorous product testing and make sure that all wicks meet basic safety standards, such as length and diameter limits as well as a list of approved wax materials. Finally, many manufacturers also provide detailed instructions on proper use of their products which outlines important do’s and don’ts of candle making.
Examine trends in candle making
Currently, the candle making industry is experiencing an upward trend with new scents, styles and trends emerging each year. Many manufacturers are launching new products such as wax melts, scent shots and even soy-based candles to meet the demand of customers. Furthermore, customers today are more conscious about their purchases, therefore many candle makers have begun offering eco-friendly options such as recyclable packaging and organic waxes.
Customers can capitalize on these trends by customizing their own candles with various scents, colors or even decorative items. Additionally, making use of eco-friendly supplies can benefit the environment while simultaneously providing a unique product that other makers may not offer. Customers could also take advantage of tips and techniques by signing up for workshops offered by makers or the manufacturer’s equipment supplier. By educating themselves on how to create unique candles using modern equipment and techniques, makers can increase their ability to effectively target their desired customer base.
Detail a step-by-step process for working with a Manufacturer
1. Send a detailed inquiry to manufacturer: This is the first step and it involves customers sending in an inquiry that outlines their exact requirements for candle-making equipment. This would include details such as the type of candles needed and associated materials, quantity, unique features, delivery timeframe, lead time, packaging preference etc.
2. Respond with quote: Upon receiving an inquiry from a customer, the manufacturer should provide an itemized proposal that includes pricing information on all components of their order.
3. Sign contract or purchase order: After agreement has been reached between the customer and the Candle Making Equipment Manufacturer on all parts of their order – details such as delivery timeframes, returns policies, custom services etc – both parties should sign a contract or purchase order providing binding agreement between them.
4. Payment processing: The customer should process payment according to the agreed terms – either up front or at delivery depending on preference – including product cost minus discounts/rebates offered by Manufacturer if applicable.
5. Manufacturing & Delivery: The Manufacturing then gets to work on producing the requested products including components according to the agreed standards or specifications outlined in the contract/purchase order. Once items are ready they will be packaged and shipped out using either third-party shipping companies or their own fulfillment teams according to setup.
6. Post Delivery Services: Finally once items have been delivered there may be need for after sales services such as installation assistance which may be included in initial agreed terms or charged separately/later depending on contractor preferences
Address customer questions & concerns
Answering customer questions and addressing concerns is a critical aspect of working with a Candle Making Equipment Manufacturer. Customers should feel comfortable asking questions and voicing their concerns in order to make sure they get the best prices and delivery times.
When it comes to prices, customers should inquire about bulk ordering discounts, especially when ordering in large quantities. Additionally, customers can often save on shipping costs by choosing flat rate or otherwise cheaper options. Customers can also ask if there are any seasonal discounts offered by the manufacturer on their candle-making equipment.
When it comes to delivery times, customers should confirm when their expected delivery is before placing an order. The manufacturing company should provide information on how long it takes for orders to be processed and fulfilled, as well as detail any potential delays that may occur due to weather or other factors that are out of their control. Additionally, customers should ask if there are any options for expedited delivery and confirm what those terms might include (e.g., additional fee).
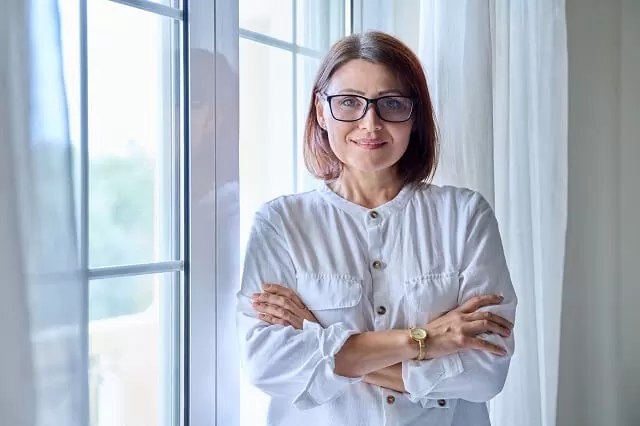
Welcome to my candle making blog! In this blog, I will be sharing my tips and tricks for making candles. I will also be sharing some of my favorite recipes.