Introduction
The history of candle making manufacture dates back to ancient civilizations, when candles were primarily used to produce light. In recent years, the popularity of candles has increased significantly as they have come to symbolize peace, relaxation and celebration. They offer consumers a unique way to decorate their homes or create an inviting atmosphere for guests. Candle making has become a popular choice for home business entrepreneurs and professional candle makers alike.
The benefits of entering the candle making market include low start-up costs, relatively few tools and materials needed and the ability to customize products according to customer demand. Furthermore, many candle makers find the craft enjoyable due to its creative aspects. However, it’s important to note that there are certain challenges associated with this line of work such as production costs, competition and marketing skills which must all be mastered in order for a business venture to be successful.
The candle making manufacturing process requires a variety of steps in order for a product to be produced efficiently and successfully. The most common methods involve melting pre-moulded wax blocks or pouring hot liquid wax into metal molds in order to form individual candles. Once cooled, various scents and decorations may be added in order for each item to bear the desired look. Lastly, finished products must pass through an inspection process before being packaged and shipped correctly so as not to damage them during transit.
Different Types of Candle Manufacturing Methods
The candle making manufacturing process can involve several different types of methods. One of the earliest and most traditional methods is dip molding, which involves repeatedly dipping a wick into liquid wax until the desired thickness is achieved. This method is used to create taper candles and cylindrical pillars. Another popular method is container wax pouring, which involves pouring melted wax into a container, typically a metal tray or tin, and letting it cool until it has solidified. Container wax pouring can be used to create simple shapes such as cubes, cones, and domes. The cold process method uses heat resistant molds that must be filled with a combination of solid wax and essential oils slowly blended in stages over a period of time to set properly. Finally, the candle rolling method is used to make rolled beeswax candles in conical shapes without the use of any molds.
Comparing Wax Types Used in Candle Manufacturing
When it comes to candle manufacture there are a variety of wax types available for use. Some of the most common include paraffin, beeswax, soy wax and gel wax. Each one has its own unique properties that make it suitable for different applications including scented candles, container candles, votive candles and more. Paraffin is the most widely used as it is affordable and easy to mold. It produces a bright and stable flame when lit; however, paraffin releases some pollutants when burned so this should be taken into consideration.
Beeswax is another popular option for candle making; the main benefit of using beeswax is that it produces a natural sweet smell as well as emitting fewer pollutants compared to paraffin when burning. The downside with beeswax is that it’s slightly more expensive than paraffin and tends to melt at lower temperatures causing weak candles over time if not stored in an area with low temperatures. Soy wax has similar benefits to beeswax but at an even higher price tag, plus soy doesn’t create the same vivid flames as other waxes do. Then there’s gel wax which is made from a combination of resin, mineral oil and plastic polymers creating a semi-transparent product with a longer lasting flame than other waxes while also emitting less pollutants when burned. While costlier than traditional waxes like paraffin; gel wax also helps create unique special effect candles due to its viscosity.
When looking for the best type of candle making options, you have to assess all factors such as cost on manufacturing process or final product cost / retail price , the quality of your end product (flame stability and longevity) pollution output (if applicable) melted texture / burning behavior or other effects based on aesthetic preferences that your desired finished product needs from each type of these different candlemaking methods . With careful examination you can choose a solution that fits your end goals while still complying with relevant safety standards (such as having no airborne pollutants).
Understanding the Candle Making Process and Equipment Needed
The traditional process of candle making dates back to ancient times, however, modern-day candle makers have access to a variety of efficient and effective equipment that can help make the manufacturing process easier and more efficient. Common equipment needed for candle making includes wax melters, fragrance pouring pots, wicks, wick holders, molds, thermometers, and measuring cups.
Wax melters are essential when it comes to melting wax down to the desired consistency prior to adding any additional ingredients such as colorants or fragrances. Pouring pots are necessary for their ability to hold up to 3 pounds of melted wax at once. Different types of wicks are available, depending on the ultimate design and size of the candle desired. Wick holders provide an added level of safety when setting up a candle for pouring by keeping the wick centered in place in the mold. Molds come in all shapes and sizes including round cylinder, tapered cylinder, square cube or just about any other custom shape imaginable when creating products from scratch. Accurate temperature readings are easily attained with a thermometer inserted into the melting wax during production runs. Finally, measuring cups are useful for ensuring each component used maintains proper ratios throughout the entire process.
Sufficiently understanding these tools is important for producing high-quality candles that align with customer expectations over time with consistency in mind. Utilizing only quality materials and components will also lead to higher customer satisfaction levels than products produced with poor quality raw ingredients could offer. Furthermore, proper equipment maintenance is essential for eliminating potential contamination risks while avoiding early breakdowns and costly repairs throughout the process.
Preparing the Materials and Environment for Safe Candle Making
Before beginning the candle making process, it is essential to ensure that the environment and materials used for manufacturing are safe. This includes turning off any heat sources like open flames or stoves, as well as securing any flammable items that might be nearby. All containers and tools must also be cleaned of dirt and grease. It is important to ensure that the work area is well-ventilated because of wax fumes. Additionally, all materials should be checked for quality and safety before use, such as ensuring that any dyes or fragrances are fragrance-free and non-toxic. Finally, all safety equipment such as goggles and gloves should be worn while working with hot wax or melting ingredients. Once all these preparations are complete, candle makers can move on to the next step of the candle making process.
Pouring, Designing and Cooling the Wax for Creative Wrapping
The candle making manufacturing process begins with melting the wax to a liquid form in a large pot. Then it is poured into metal or plastic molds of varying shapes and sizes. Depending on the design desired, dyes, chemicals, scents and other colored elements can be added to the melted wax for customizable results. After that, wicks are placed inside each mold then the mixture is left to cool down and become solidified.
Once cooled, designing kicks in as various decorations and personalizations such as logos or lettering on the candles can be painted on with special wax-based paints or glues like beeswax. For creative wrapping options, paper labels can be printed and applied, and different kinds of packaging materials like shrink wraps and cellophane bags can also be used. Each candle is then checked for imperfections before being ready for sale.
Adding Scents, Color and Enhancing Additives
Candle making involves a careful addition of scents, colors and enhancing additives. This task requires the use of solvents that allow for the mixing of inks and oils into waxes, as well as specialty techniques for scent holding, embedded objects and color intensity. It is essential to create a well-balanced formulation so that the finished product does not put off an overly strong smell or produce too much smoke. Achieving the desired outcome may require small tweaks to the ingredients that can only come from experience.
To begin, precise amounts of wax must be weighed out using eitherDigital scales or volumetric measuring cylinders depending on the desired end results. Once this is complete, it must be heated gently until it melts completely without being over processed. Once melted, dyes and/or pigments can be added to give it a color. For more complex mixtures such as embedding objects in candles special techniques such as pressing techniques are used to assist in the process of their placement into the molded candle form before cooling and hardening starts.
The final step before packaging is adding scent or aromas to enhance the entire product’s appeal; this is usually done with essential oils which add natural scents to candles whereas Synthetic Fragrance Oils add additional smells like fruits and florals that may not otherwise be available in natural form. This combines with manipulating wick size will help further control how strong each candles aroma is when lit. The completed product will then pass through quality assurance testing where all measurements are taken making sure weight, size dimensions and appearance all meet federal standards prior to packing up in custom boxes or retail packaging ready for shipping destination.
Finishing, Packaging, Labeling and Shipping of the Candles
Once the candles are made, they must then go through a finishing process. This may include dusting off any excess wax that may have been produced during the pouring, trimming of the wick and making sure each candle is aesthetically pleasing. The finished candles are then packaged in boxes or other forms of protective wrap, labels are added to ensure proper tracking and product information is included. After all of those processes have been completed, the candles can be shipped to their respective locations via freight or courier services.
Essential Legal Considerations When Starting a Candle Making Business
When starting a candle making business, it is essential to consider any legal considerations that may be necessary for the successful operation of the company. Depending on several factors (including jurisdiction and size of the business) obtaining certain licenses and permits may be required. Additionally, familiarizing yourself with both state and federal laws related to owning a business is important. It’s especially important to understand laws related to fire safety; depending on the area, it might be necessary to obtain specialized licenses or certifications in order to manufacture and/or sell candles. Safety precautions should also factor into your legal considerations; potential customers must feel assured that their purchase is not simply aesthetically pleasing but safe as well. Consider looking into any governing body who can provide guidance or assistance in developing safety protocols and standards for your product. Finally, it’s important to make sure that you have all appropriate insurance coverage; this will help protect you, your property, and others from liability should anyone use your products unwisely.
Conclusion
Benefits: Candle making is an engaging, creative and rewarding hobby which provides financial benefits with properly designed candles, successful marketing strategies and a retailer base. It can give you the opportunity to express your creativity while in turn producing something meaningful that many people appreciate and value. Furthermore, you can start a candle-making business from home at low cost as there are few upfront start-up costs.
Challenges: Candle making does require some technical knowledge and understanding of candle chemistry. This includes how to calculate wax for desired yield and size, proper scent levels for candles as well as any wax additives used in formulating candles in order to get the right burn characteristics such as hot or cold throw. Additionally, it is important to make sure the wick is of appropriate size depending on the type of wax being used and the diameter of the container.
Opportunities: One opportunity in candle making manufacturing is developing scented candles that appeal to customers which include options such as aromatherapy, natural oils, personalized fragrances or unique packaging designs. Additionally, providing an option for customization could offer customers more choices like personalized labels or designs giving them a chance to express their own stories provokes greater connection with a brand’s story that drives loyalty among consumers.
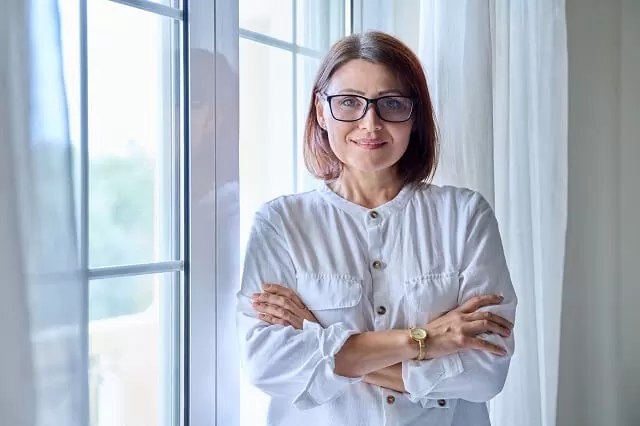
Welcome to my candle making blog! In this blog, I will be sharing my tips and tricks for making candles. I will also be sharing some of my favorite recipes.