Introduction
Candle making as an industry dates back to the 19th century. Candle wick factories play an important role in producing the wicks needed to make candles and provide a link between the process of candle making and the technology used today. Wicks can be produced from a variety of materials such as cotton, rayon, paper, or even stainless-steel wires that are treated with various chemicals. The sensitivity and manipulation of combustion used when creating candles is highly dependent on the choice of material for the wick.
Wick factories create pre-treated candle wicks using loops, plaiting, taping and dipping processes. Making fine adjustments by manipulating factors such as weight and weave densities is crucial for successful candle production. Candles made with lower quality wicks may produce more smoke or have inconsistent burning performance due to the impurities present in lesser quality materials. This can be avoided by using premium grade materials that offer superior performance with less ‘sooting’ when burning and are flame retardant for enhanced safety during use.
Factories also specialize in areas like wax dip technology which also helps enhance product quality by coating seeds in wax before being put into production mode. Further advancements allow production lines to handle non-round wicks while negative twists eliminate slackness within each individual loop twist, thereby enabling increased speed of wax flow even at high speeds on production machines while decreasing overall cost associated with manufacturing equipment.
Historical Perspectives on Wick Factories
Wick factories have been in use for centuries, with records indicating that a type of wick manufacture was first mentioned as far back as 17th century France. This rudimentary form of candle making equipment was developed and improved upon over the years to provide a solution to the problem of how to reliably produce long-lasting wicks. During this period, most wicks were made by hand with beeswax or animal tallow and held together by loosely twisted threads.
By the late 19th century, however, technological advancements allowed wick factories to emerge and become an important part of the industrial revolution. These specialized plants established dedicated production lines which could produce large quantities of consistent quality wicks quickly and cost-effectively. In addition, improved materials such as cotton and linen were introduced that produced better burning results with little smoke or odor.
Today’s modern wick factories have evolved considerably from their earlier counterparts. Automation has been introduced on many levels, allowing for increased speed and accuracy in product creation while also reducing labor needs. Machines are now capable of winding precise lengths of wicking material around wire cores at rapid speeds, removing human error from the equation altogether. The advent of electric powered spooling tools further accelerated production capabilities, leading to greater availability and more options for consumers worldwide.
Varieties of Wick Factories
Candle making wick factories manufacture a variety of wicks used to make candles. The type of wick used affects the burning characteristics of the candle, such as how long it will burn and how evenly distributed will be. Types of wick factories vary by the materials they use, fabrication technique, and size.
Common types of material include cotton, paper, wood, tinned metal and glass-coated threads. Wood is highly appreciated because of its self-trimming effect; nonetheless, there are certain limitations associated with using wooden wicks. Fabrication techniques can be divided into four categories: braiding/weaving; winding/wrapping; linking/knotting; and twining/twisting.
Wick sizes can have diameters ranging from 0.2 mm to 3 mm depending on style and flame size requirements for each specific candle and application. Assembled size (length) depends on where to anchor the tabs and other factors such as length required for each particular application within the chosen container’s length & wall thickness.
Overall, choosing a suitable wick factory is an important factor when producing high quality candles that burn evenly with consistent printability on wax candles in possible all shapes and sizes customized according to customer needs.
Candle Making Supplies
Candle making is a great hobby that can be enjoyable and therapeutic to do. To create good quality beeswax candles, making sure you have the right supplies is key. The essential component of any candle is the wick, which allows for the wax to be burned in a controlled way. Candle making wick factories produce different types of wicks for different kinds of candles such as paraffin, soy-based, palm-based, and beeswax candles. The most important factor when purchasing from a candle making wick factory is to determine if the product meets your particular needs. Some tips for selecting a quality product include: checking the diameter size or length of the wick as well as its construction; looking at how many strands are used; considering the type of fiber used for the wicking portion; assessing its burning qualities; and noting any flame size requirements needed depending on your desired candle design. In addition, it is important to take into account both the upfront costs associated with purchasing wicks from a factory as well as ongoing maintenance bills, since some candle supplies (such as specialized dressings) may need to be purchased on an occasional basis in order to ensure optimal performance.
Candle Wick Crafting Process
The candle wick crafting process begins with thoroughly cleaning the thread and cotton necessary to form a good candle wick. This may involve soaking it in warm soapy water and scrubbing off any dirt or debris. Once the material is cleaned, the worker dips some of the clean fibers into wax and attaches a weight, usually made of lead, to keep the wick weight at the desired length. The worker then winds the fibers around a spindle, pulling them nice and tight.
The next step involves dipping the wick multiple times into hot freestanding liquid wax or melted wax from bar form. This allows for further buildup on the fibers creating extra tension that helps keep the flame burning evenly as it moves up from bottom to top within a candle.
Once satisfied with how many layers of wax have been applied, workers trim any excess threads or imperfections from all sides using scissors or tweezers. After this step is complete, workers inspect each wick visually for consistency before wrapping it up for shipment to places all around the world!
Benefits of Wick Factories
Wick factories can offer a wide range of benefits when used for candle making. The wicks produced in these factories are typically crafted using only the highest quality waxes, wicks, and other materials, resulting in consistently reliable candle burning performance. Additionally, when compared to handmade or hand-stitched wicks available in standard craft stores, industrial factory-made wicks are generally wider and longer lasting. This means that candles created using these wicks burn more efficiently and will likely last longer due to the higher quality materials employed during production. Factory-created wicks also cost considerably less than handcrafted alternatives when purchased in bulk, making them an ideal choice for large scale manufacturers. Further, since they are all made according to specific standards, you can rest assured that your candles will have a consistent appearance throughout their lifetime no matter where on the planet they’re made. Finally, thanks to the sheer variety of sizes available for each type of wick factory-made candles allow for greater flexibility when it comes to experimenting with different designs or sizes of candles; something which would be impossible with some homemade options.
Safety and Regulations
Safety regulations and standards are essential parts of candle-making wick factories. Safety protocols should be created that cover everything from fire hazards to chemical risks. Fire hazards can result in fires and explosions, while chemical risks involve exposure to hazardous substances. To reduce the likelihood of such disasters, the use of protective equipment like heat-resistant gloves, welding helmets, and safety goggles is recommended when working with waxes or operating machinery.
Additionally, ventilation systems must be in place to properly vent any smoke produced from melting wax and soot from burning wicks. It is also important for workers to practice safe handling techniques during production processes such as reinforcing wicks for lanterns or dipping wicks into wax baths. In some instances, these processes require heating elements and high temperatures that can cause burns or toxic fumes if not handled properly. Adequate ventilation systems must be installed throughout the area where production processes occur to ensure safety standards are met.
Finally, understanding of the types of materials used in the factory environment is key for ensuring safety at all times. For example, eliminating metal material near burners can help prevent sparks caused by metal against metal contact which could potentially start a fire. Following safety regulations includes being aware of other dangerous toxins like formaldehyde or benzene which may be released during processes and taken precautions to reduce exposure risk as much as possible through proper ventilation systems.
Future of Candle Making Wick Factories
Candle making wick factories have been around for many years, providing a reliable and safe source of wicks to candle makers. In recent years, the industry has evolved to meet the changing needs of the ever-growing candle-making industry. This includes focusing on production safety, sustainability, and developing innovative and efficient production methods. As such, there is considerable potential for increased innovation and efficiency in this sector that could propel it into the future.
One potential avenue for this could be through improved automation and cleaner materials to reduce human handling errors and produce wicks more quickly. Additionally, creating custom tools and fixtures that allow for easier customization of waxes or fragrances could offer increased variety for customers in quick turnaround times. Additionally, researching new coatings or materials to make wicks last longer or burn brighter can result in higher customer satisfaction ratings. In addition to these improvements, finding ways to recycle or reuse materials from production processes can lead to greater cost savings as well as an eco-friendly approach to business operations.
As candle-making becomes increasingly popular with more people around the world turning to creative hobby outlets during lockdowns due to Covid-19, it is also important for wick factories to remain agile enough to meet increased demand without compromising on quality and safety standards. This includes maintaining adequate stocks of raw materials while investing in research into faster manufacturing techniques such as 3D printing or laser cutting options that could provide quick turnarounds without sacrificing quality. Finally, introducing trending scents or dyes into wax can further appeal both seasoned candle makers and those newer to the market with exciting colours and scents at their fingertips.
In conclusion, there are numerous opportunities available for improvement in the candle-making wick factories sector which could bring them firmly into 2020s and beyond by embracing automation technology & clean materials allowing quicker turnarounds as well as increasing output efficiency whilst also exploring new avenues of supply such as creating interesting fragrances & dyes along with sustainable material reusing/recycling efforts all creating a yet brighter future for Candle Making Wick Factories globally!
Conclusion
The importance of wick factories in candle making cannot be overstated. Without them, candles would not burn properly and the quality of the light they provide would be greatly reduced. The blog post went into detail about the various techniques used to make wicks, from spinning cotton fibers to winding metal around a core. It also discussed the research and development used to ensure that the right combinations of materials are used to create high performing wicks. Moreover, it highlighted the applications for specific types of wicks depending on the desired effect—for example beeswax or paraffin-based candles require different sizes of wicks compared to soy or soy blend candles. Finally, it explained why a factory or production line setting is preferred for larger scale candle manufacturing. In conclusion, candle making wick factories play a critical role in candle production by creating quality wicks that will burn cleanly and evenly for optimal performance and safety.
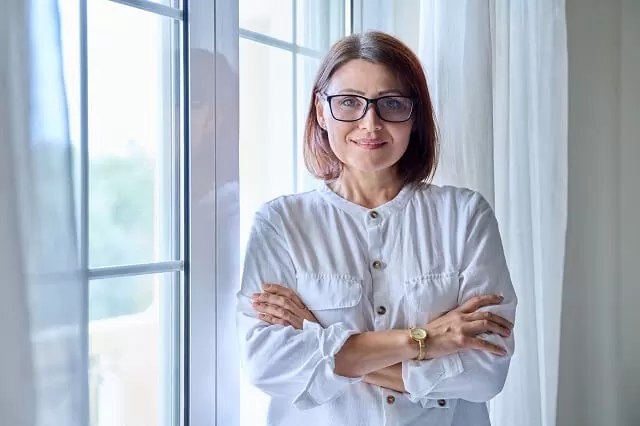
Welcome to my candle making blog! In this blog, I will be sharing my tips and tricks for making candles. I will also be sharing some of my favorite recipes.