Are you interested in venturing into the candle making business? Whether you are just starting or looking to upgrade your production process, investing in a fully automatic candle making machine could be the game-changer you need. This revolutionary piece of equipment has transformed the way candles are manufactured, making the process more efficient and cost-effective.
A fully automatic candle making machine is designed to streamline the production process by automating various tasks involved in candle making. From mixing and melting wax to molding and cooling the candles, this advanced machine can handle it all with minimal human intervention. As a result, businesses can significantly increase their production capacity while reducing manual labor costs.
In this article, we will explore the benefits of investing in a fully automatic candle making machine and how it works. We will also discuss the top features to look for when choosing a machine for your business, provide tips for selecting the right one, and showcase successful case studies of businesses that have embraced this technology.
Additionally, we will delve into maintenance and care for these machines and ponder on the future of candle making with fully automatic machines. So if you’re considering taking your candle-making business to the next level, keep reading to discover everything you need to know about fully automatic candle making machines.
The Benefits of Investing in a Fully Automatic Candle Making Machine
Investing in a fully automatic candle making machine can offer numerous benefits for candle manufacturers and businesses. Here are some key advantages of utilizing this advanced technology:
Increased Efficiency and Productivity
A fully automatic candle making machine can significantly boost the efficiency and productivity of your candle production process. With the ability to perform multiple tasks automatically, such as wax melting, pouring, cooling, and even packaging, these machines can streamline the entire manufacturing process. This means that you can produce a larger volume of high-quality candles in a shorter amount of time, ultimately increasing your output and meeting consumer demands more effectively.
Cost Savings
While the initial investment in a fully automatic candle making machine may seem significant, it can actually lead to long-term cost savings for your business. By automating various production tasks, you can reduce the need for manual labor and minimize human error, which ultimately lowers labor costs. Additionally, the streamlined production process results in less wastage of raw materials, further contributing to cost savings over time.
Improved Quality Control
Fully automatic candle making machines are equipped with advanced technology that ensures consistent quality throughout the production process. From precise wax pouring to uniform cooling and shaping, these machines can help maintain higher standards of quality control compared to traditional manual methods. This not only enhances the overall quality of your candles but also reduces the likelihood of defects or inconsistencies in your products.
How a Fully Automatic Candle Making Machine Works
A fully automatic candle making machine is a revolutionary piece of equipment that has streamlined the candle production process for many businesses. This section will explore how these machines work and the specific mechanisms that allow them to efficiently produce high-quality candles.
Here are the key steps involved in the operation of a fully automatic candle making machine:
- Wax Melting: The process begins with the melting of the wax, which is an essential component of candle making. The machine heats the wax to the optimal temperature for pouring into molds.
- Mold Filling: Once the wax reaches the desired consistency, it is automatically poured into molds of various shapes and sizes. This step is crucial for creating a wide range of candle designs.
- Cooling and Solidifying: After filling the molds, the machine ensures that the wax solidifies and cools down at the right pace. This is important for achieving uniform and flawless candles.
- Unmolding: Once the candles have solidified, the machine automatically releases them from the molds, ready for further processing or packaging.
The efficiency and precision of a fully automatic candle making machine can significantly boost production capacity while maintaining consistency in candle quality. These machines also offer programmable controls that allow for customization according to specific production requirements, making them versatile tools for businesses in the candle-making industry.
Overall, understanding how a fully automatic candle making machine works provides valuable insight into its capabilities and potential impact on a business’s production processes. With their advanced functionalities and automated operations, these machines have undoubtedly transformed the way candles are manufactured on a commercial scale.
Ultimately, investing in this state-of-the-art technology can help businesses meet consumer demands more effectively while optimizing their overall production efficiency.
Top Features to Look for in a Fully Automatic Candle Making Machine
When considering investing in a fully automatic candle making machine, it is important to take into account the specific features that will best suit your business needs. One of the most crucial features to look for is the production capacity of the machine. Different models come with varying levels of production output, so it is essential to assess how much volume you plan on producing and choose a machine that can accommodate your requirements.
Another important feature to consider is the versatility of the machine. A good fully automatic candle making machine should be able to handle different types of candle designs and sizes. This will allow you to expand your product line and cater to a wider range of customer preferences, ultimately maximizing your business potential.
Additionally, efficiency and automation are key features to look for in a fully automatic candle making machine. The ability of the machine to minimize manual labor and streamline production processes can significantly improve productivity and reduce operational costs. Look for machines that offer advanced automation technologies such as programmable settings, self-cleaning functions, and real-time monitoring capabilities.
In summary, when searching for the right fully automatic candle making machine for your business, focus on key features such as production capacity, versatility, and automation capabilities. By carefully assessing these features and how they align with your specific business needs, you can make an informed decision that will contribute to the success and growth of your candle making enterprise.
Features | Description |
---|---|
Production Capacity | Determine the volume of candles the machine can produce |
Versatility | Evaluate its capability to handle various candle designs and sizes |
Efficiency and Automation | Look for advanced automation technologies that can minimize manual labor and streamline production processes |
Tips for Choosing the Right Fully Automatic Candle Making Machine for Your Business
When it comes to choosing the right fully automatic candle making machine for your business, there are several important factors to consider. Making the investment in a fully automatic candle making machine can significantly improve your production process and overall efficiency. Here are some tips to help you make the right choice for your business:
Production Capacity
One of the most important considerations when choosing a fully automatic candle making machine is its production capacity. You’ll need to assess your business’s current and anticipated future production needs. Consider factors such as demand trends, seasonal variations, and potential for growth. A machine with higher production capacity may require a larger initial investment, but it could be more cost-effective in the long run if it can meet your future needs without needing to be replaced.
Customization Options
Consider whether the fully automatic candle making machine offers customization options for different types of candles. Some machines may have limited flexibility in terms of candle size, shape, and color variations, while others may offer more versatility. If you plan to produce a wide range of candle products, look for a machine that can accommodate these varying needs.
Quality and Reliability
It’s crucial to invest in a fully automatic candle making machine that is built with quality materials and components to ensure its durability and long-term reliability. Research different brands and models, read customer reviews, and consider reaching out to other businesses using similar machines for their feedback. A reliable machine will minimize downtime due to maintenance or repairs, keeping your production line running smoothly.
By carefully considering these factors when choosing a fully automatic candle making machine for your business, you can make an informed decision that will benefit your production processes and overall operations.
Case Studies
Many businesses have experienced significant success after investing in a fully automatic candle making machine. One such example is a small start-up candle company that saw a major increase in production and revenue after transitioning from manual to fully automatic candle making. With the new machine, the company was able to produce a larger volume of high-quality candles in a shorter amount of time, meeting the growing demand from their customers and expanding their market reach.
Another case study involves an established candle manufacturer that upgraded their production line with a fully automatic candle making machine. The result was not only increased efficiency and productivity, but also improved product consistency. This led to higher customer satisfaction and loyalty, as well as greater opportunities for the company to enter new markets and grow their business.
Additionally, a family-owned candle business saw tremendous growth after integrating a fully automatic candle making machine into their operations. The machine allowed them to streamline their production process, reduce labor costs, and ultimately improve their bottom line. As a result, they were able to scale up their business and become major players in the industry.
These case studies demonstrate the positive impact that investing in a fully automatic candle making machine can have on businesses of all sizes within the industry. From increased productivity and efficiency to improved product quality and market expansion, it is clear that this type of machinery offers numerous benefits for those looking to take their candle making operations to the next level.
Case Study | Impact |
---|---|
Small start-up | Increased production and revenue |
Established manufacturer | Improved efficiency and product consistency |
Family-owned business | Streamlined production process, reduced labor costs, scaled up business |
Maintenance and Care for Fully Automatic Candle Making Machine
After investing in a fully automatic candle making machine, it is essential to understand the maintenance and care procedures to ensure its longevity and efficiency. Proper maintenance not only extends the lifespan of the machine but also guarantees the production of high-quality candles. Below are some important maintenance tips and care guidelines for fully automatic candle making machines:
- Regular cleaning: To keep the machine running smoothly, it is crucial to regularly clean all parts and components. This includes removing any wax buildup, dust, or debris that can affect its performance.
- Inspecting and replacing parts: Periodic inspection of key components such as molds, heating elements, and moving parts is essential. Any worn-out or damaged parts should be promptly replaced to prevent breakdowns during production.
- Lubrication: Proper lubrication of moving parts is necessary to reduce friction and wear. It is important to use the recommended lubricants and follow the manufacturer’s guidelines for lubrication intervals.
In addition to regular maintenance, proper care for a fully automatic candle making machine involves following operational protocols and safety measures. Here are some important care guidelines to consider:
- Operator training: Ensuring that operators are adequately trained in using the machine can prevent accidents and minimize mistakes that could lead to equipment damage.
- Operating environment: Maintaining a clean and suitable operating environment is important for the optimal performance of the machine. This includes controlling temperature and humidity levels in the production area.
- Safety precautions: Implementing safety measures such as emergency stop buttons, protective guards, and regular safety checks can minimize risks associated with operating the machine.
By adhering to these maintenance practices and care guidelines, businesses can maximize the efficiency and productivity of their fully automatic candle making machines while ensuring safe operations. Regular upkeep and attention to detail will ultimately contribute to a successful candle making business powered by advanced automated technology.
Conclusion
In conclusion, the future of candle making with fully automatic machines looks promising and lucrative. With the advancements in technology, fully automatic candle making machines have revolutionized the industry by streamlining production processes, reducing labor costs, and increasing efficiency. As seen from the case studies provided, businesses that have invested in fully automatic candle making machines have experienced significant growth and success.
The benefits of investing in a fully automatic candle making machine are evident, as it allows businesses to produce a higher volume of candles with consistent quality. The automation of the manufacturing process ensures precision and reliability, resulting in an increased output of high-quality candles. Additionally, the reduced need for manual labor not only cuts down on operational costs but also minimizes the margin for error.
As technology continues to advance, it is essential for candle makers to stay ahead of the curve by embracing fully automatic candle making machines. With top features such as programmable settings, multiple molding options, and rapid production capabilities, these machines offer a competitive edge in the market. By carefully choosing the right fully automatic candle making machine for your business and maintaining it properly, you can set yourself up for long-term success in the candle making industry.
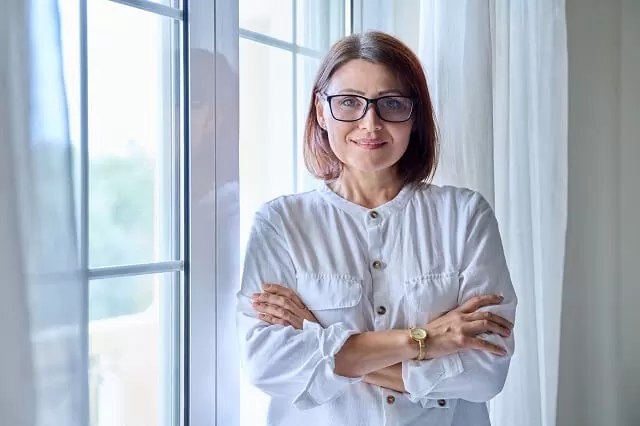
Welcome to my candle making blog! In this blog, I will be sharing my tips and tricks for making candles. I will also be sharing some of my favorite recipes.