Expand on the Introduction
Using latex for candle molds is a centuries old craft, originating in the Middle Ages when beeswax candles were made by pouring melted wax into molds crafted from sheets of animal skin or bird wings. While animal skin and bird wings are no longer commonly used to make candle molds, latex is still a popular choice among crafters and DIYers. The durability and versatility of latex makes it an ideal material for crafting homemade candle molds in many different shapes and sizes. From delicate tealight holders to soy wax jar candles, there are near infinite possibilities for traditional cylindrical styles as well as box, pyramid, pyramid hexagonal, icosahedral, and more. With a few simple tools, some patience and practice anyone can create beautiful personalized candles with unique shapes using custom-made latex candle molds.
Provide Photos
Step-by-Step Guide:
1. Gather Materials: Latex, Vaseline or Petroleum Jelly, Plastic Sheeting and Tape, Wooden Dowel or Stick
2. Wrap the Wood in Plastic Sheeting – Cut 4-6 inch strips of plastic sheeting and wrap around your wooden dowel or stick to create a mold shape that looks similar to a candle. Secure the plastic with tape.
3. Add Three Layers of Latex – Pour latex onto the wooden frame until it’s about ¼ inches thick for each layer. Allow thin coat of latex to dry for about 45 minutes before applying the next layer. Once all three layers have been applied and dried, your mold will be hard to the touch.
4. Grease up the Mold With Vaseline – Spread petroleum jelly or Vaseline to each side of your latex mold with a brush to avoid sticking when you remove your candle after pouring wax over it. Allow it to dry for another 20 minutes before use.
Tools Required:
• Latex
• Vaseline or Petroleum Jelly
• Plastic Sheeting and Tape
• Wooden Dowel or Stick
• Paintbrush
Offer Troubleshooting Advice
Troubleshooting Tips:
1. If the mold is not holding onto the latex, it may be a sign that more coating layers need to be applied. Make sure to wait between each layer until the solution has dried to ensure the best seal on the mold.
2. Refill any sunken spots or cracks in the latex to create an even finish before applying any additional layers of coating. This can help prevent any leaks later on.
3. If you find that some of your molds have uneven edges, try sealing them off with a razor blade around their perimeter for a smoother and more secure finish.
4. When filling the latex molds, allow extra liquid wax at the top as it can expand during cooling and make sure all surfaces are fully covered for an even burn when it heats up later.
5. After taking out your candles from the molds, look for any signs of leaking such as spots where wax is missing or has peeled away along its edges and make sure there are no sharp points present on its top or base that could be dangerous during use.
Highlight Alternatives
Latex is a great material for making candle molds, but there are several alternatives that can also be used. Silicone rubber is the most common alternative, as it’s non-toxic and doesn’t need to be poured into a mold. Wax-resistant plastic can also provide good results, but is more expensive than latex. Clay is another option, but it needs to be specially prepared before using with candle wax. Lastly, plaster of Paris or commercial casting plaster can also be used to make molds for candles, although the process is slightly messier and slower than other methods.
Although latex provides advantages for making candle molds in terms of cost and ease of use, each alternative has its own specific benefits. For example, silicone rubber is more flexible than latex and can handle higher temperatures without deforming or shrinking. Wax-resistant plastic provides a sturdy base that won’t warp over time and offers excellent results in regard to preserving intricate detailing. Clay is ideal if dexterity is needed during the molding process in order to create complex shapes. Plaster of Paris or commercial casting plaster produces heavier-weight candle molds which will hold up better in high temperatures compared to clay or wax-resistant plastic.
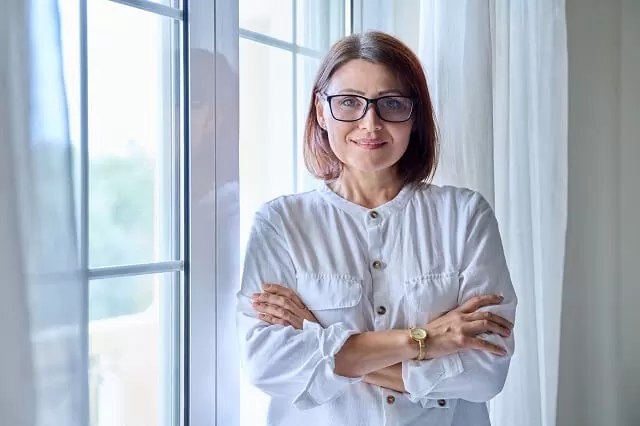
Welcome to my candle making blog! In this blog, I will be sharing my tips and tricks for making candles. I will also be sharing some of my favorite recipes.